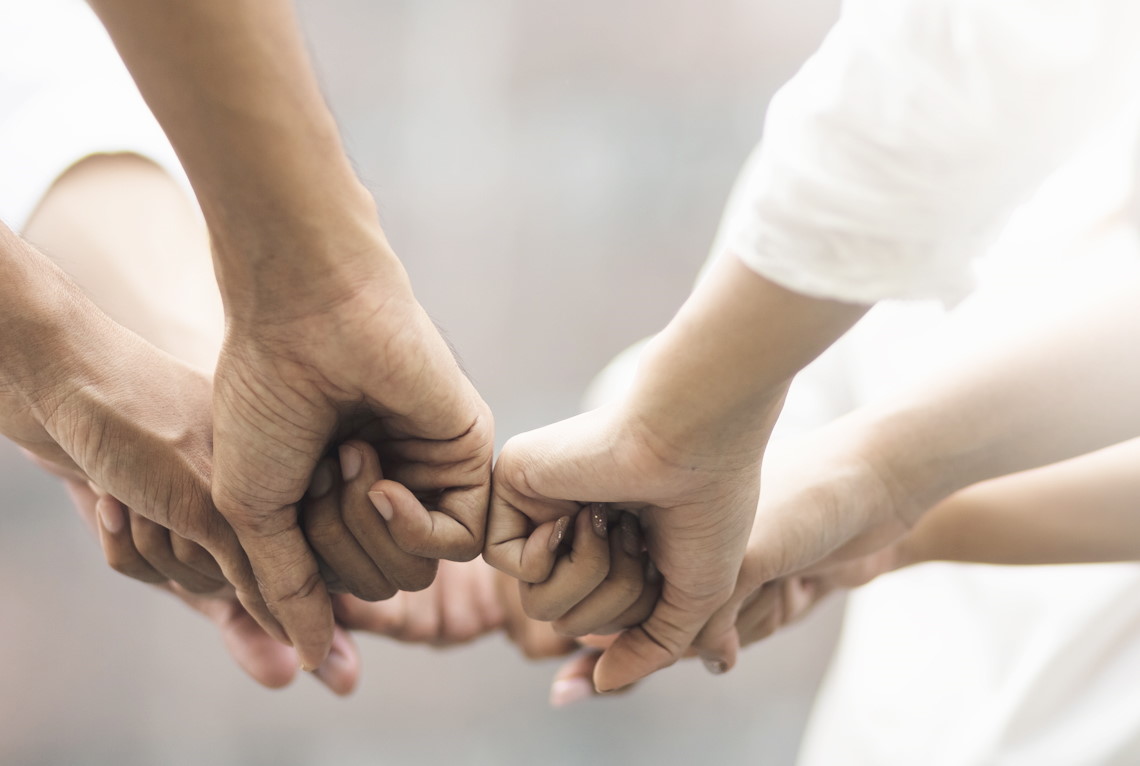
Consultation
Printing and packaging industry is one of the most complex and specialized industries that lack of proper knowledge can result in a great loss of money and time. Simin Tejarat Company with years of experience in these fields, can be your consultant in choosing the right packaging for your products.
We help you in following fields:
printing materials, laminated materials and costs, proper printing technique according to the time, quality and cost that the customers plan for, the purposeful design regarding the target market, the issues related to packaging machine, etc. Any of these issues can be a challenge on the way to achieving the goal if they are not managed properly.
Graphics
Fortunately, in recent years, the importance of design in packaging and its impact on sales of a specific product and also the conversion of a familiar product and its recrotion into an iconic product has become so obvious that there is no need to explain the role of purposeful design in entering the market.
Since the design in packaging should eventually be in the form of a printed product, knowledge and mastery of the process of flexographic and rotogravure printings is the necessary feature of a packaging designer. There are many catchy designs that are not able to attract the target customer due to the special features of each printing methods.
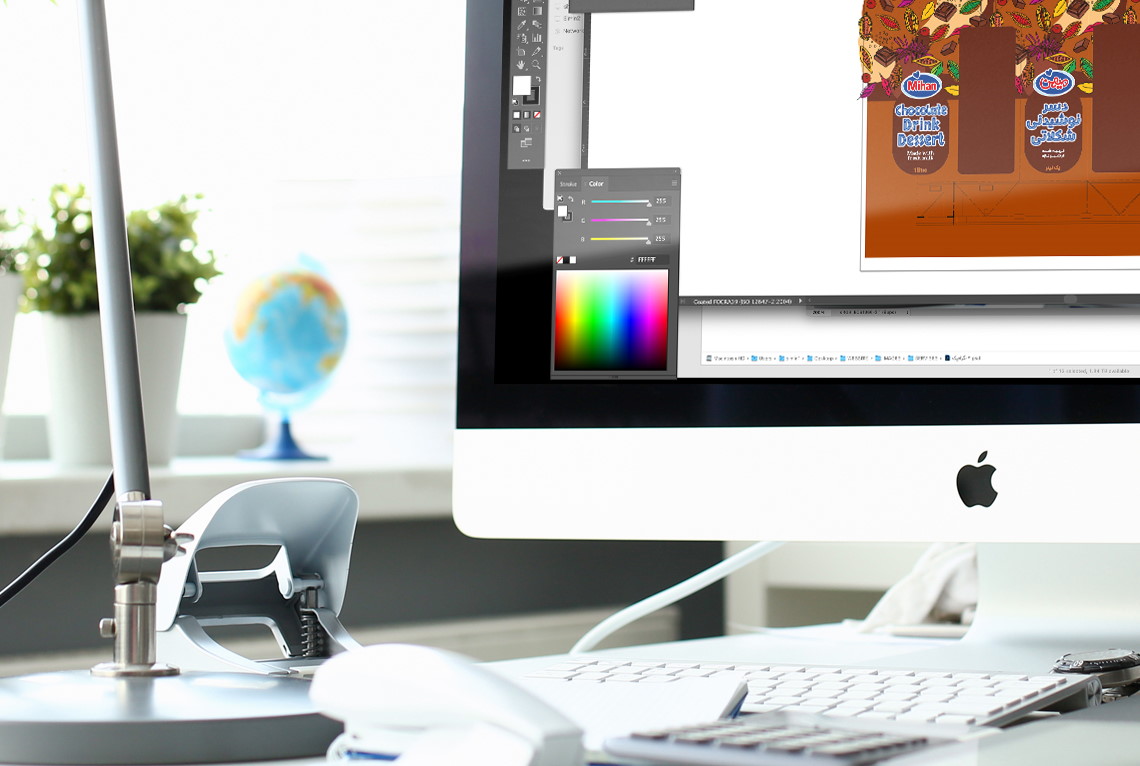
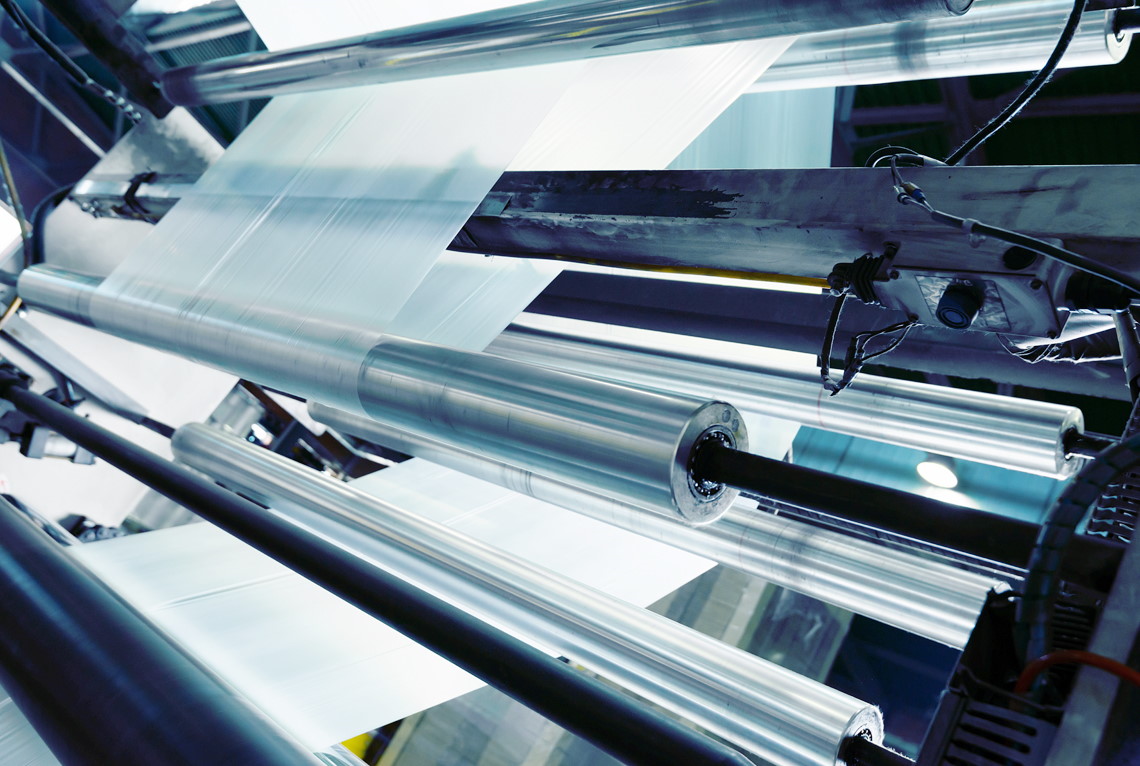
Rotogravure
Rotogravure is a high quality industrial printing process. In this type of printing, images are engraved on a cylinder. In this type of printing, specific cells are engraved on the cylinder to carry ink. Rotogravure is efficient high volume production regarding the cylinder high cost comparing plates in flexographic printing process.
Different types of films like polyethylene, polypropylene, polyester and BOPP can be printed in this system.
Flexography
Flexo printing technique is a type of printing that is done using photopolymer polytes (stereotypes) made of gelatin (elastomometer). In this type of printing, we can print on a variety of polymer films, aluminum-foil, papers, self-adhesive labels and even metal cans. Flexo printing is very popular due to its time efficiency in designing, plate production and printing process, as well as lower costs comparing rotograver printing. Nowadays, new technologies resulted in significant improvement in this type of printing.
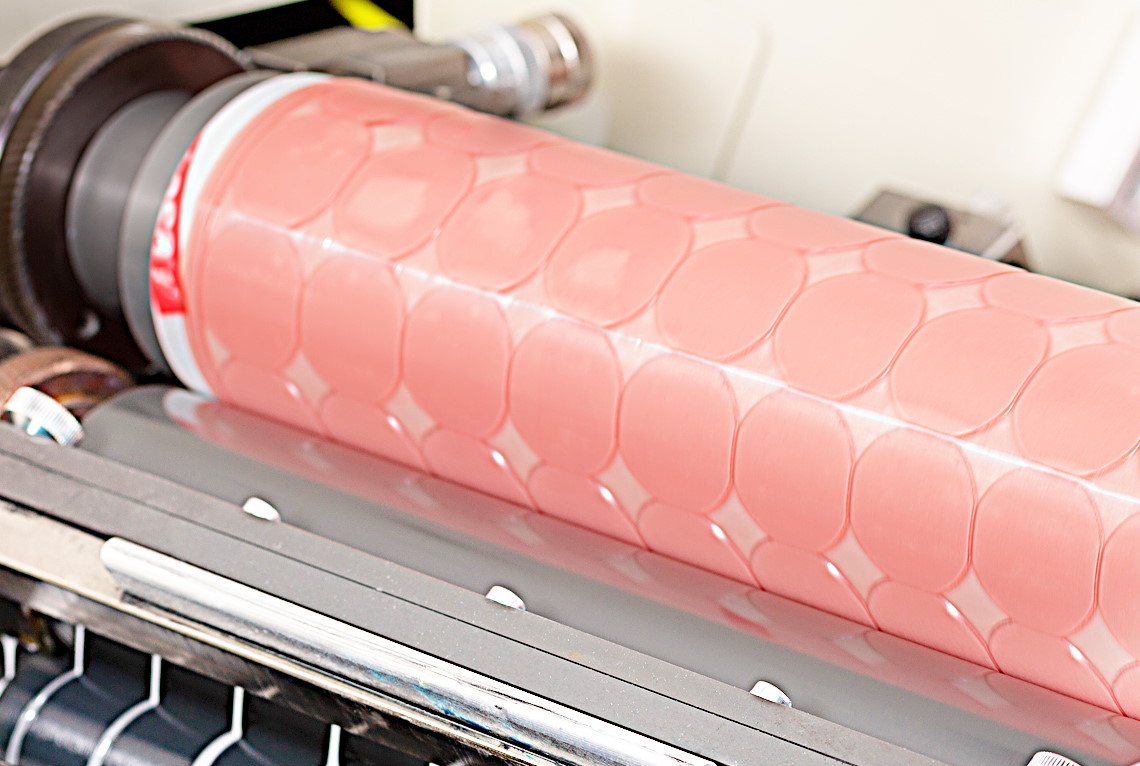
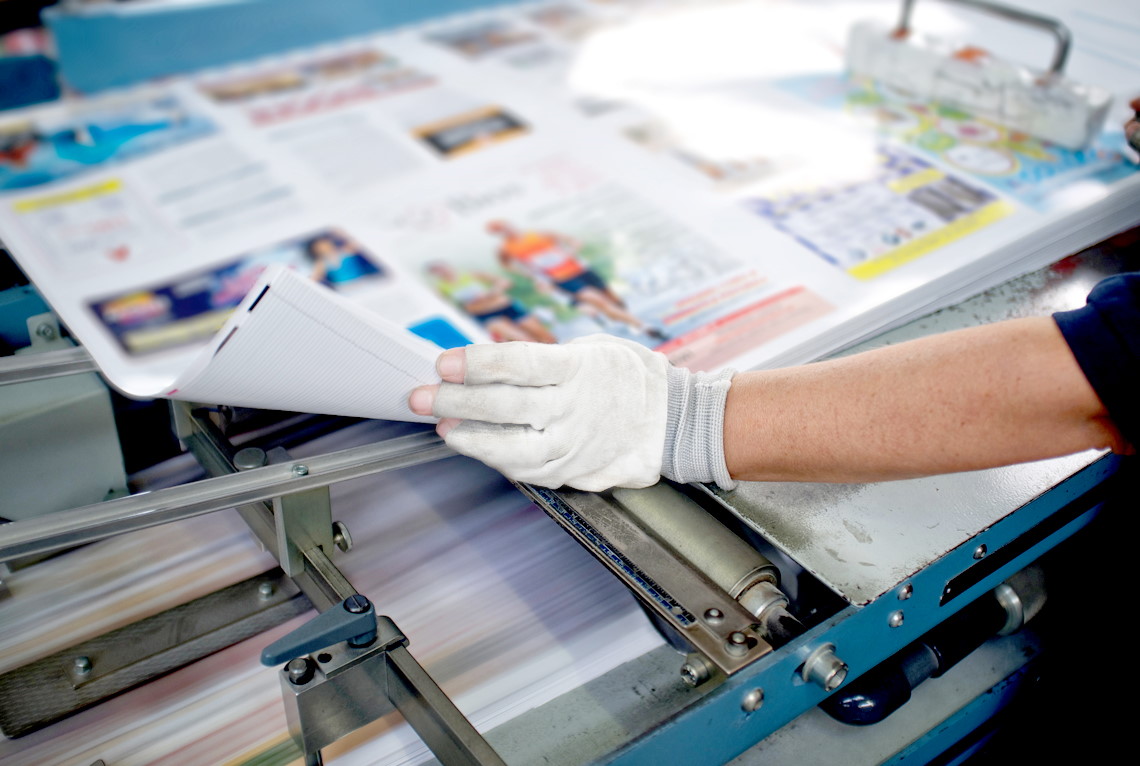
Offset Printing
Offset printing is the most common and well-known type of printing method. Offset printing is used not for printing on BOPP films, but for printing on paper and cardboards to produce laminated carton boxes as well as a wide variety of hard packaging for food products. For instance, Calippo printing is done by offset printing, with food-grade inks and on special paper for ice cream packaging.
Cylinder
Raw cylinder is made of steel, seamless, in different diameters, which is prepared after various operations of lathing and balancing.
Cylinder overlay is from chromium and copper is used beneath. After preparing the cylinder, the graphic file is engraved by the laser. The deeper the engraved cell, the more ink is transferred. To print a design, one cylinder is made per color.
Quality of chromium, implementation of the design on the cylinder, creating proper angles and selecting the amount of color transmission are among the most important and influential factors in the cylinder production process.
Although, nowadays, due to advanced technologies, the construction of high quality cylinders has become easier, but the presence of a professional production team necessary.
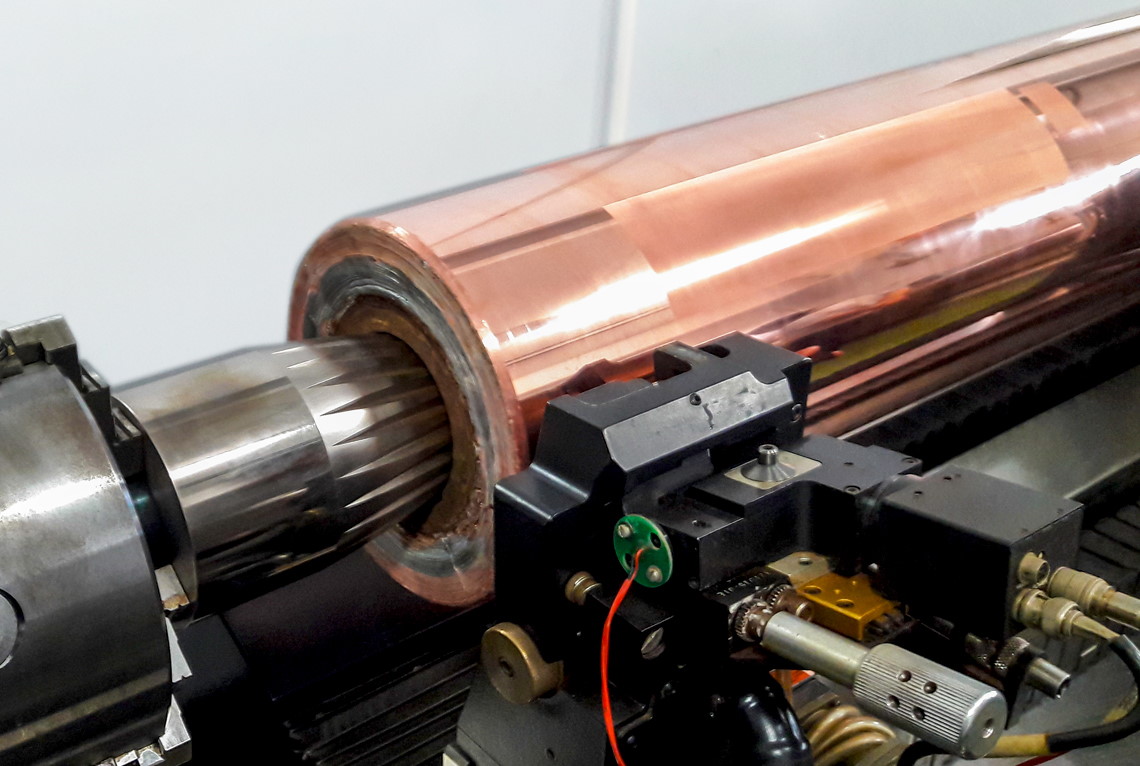
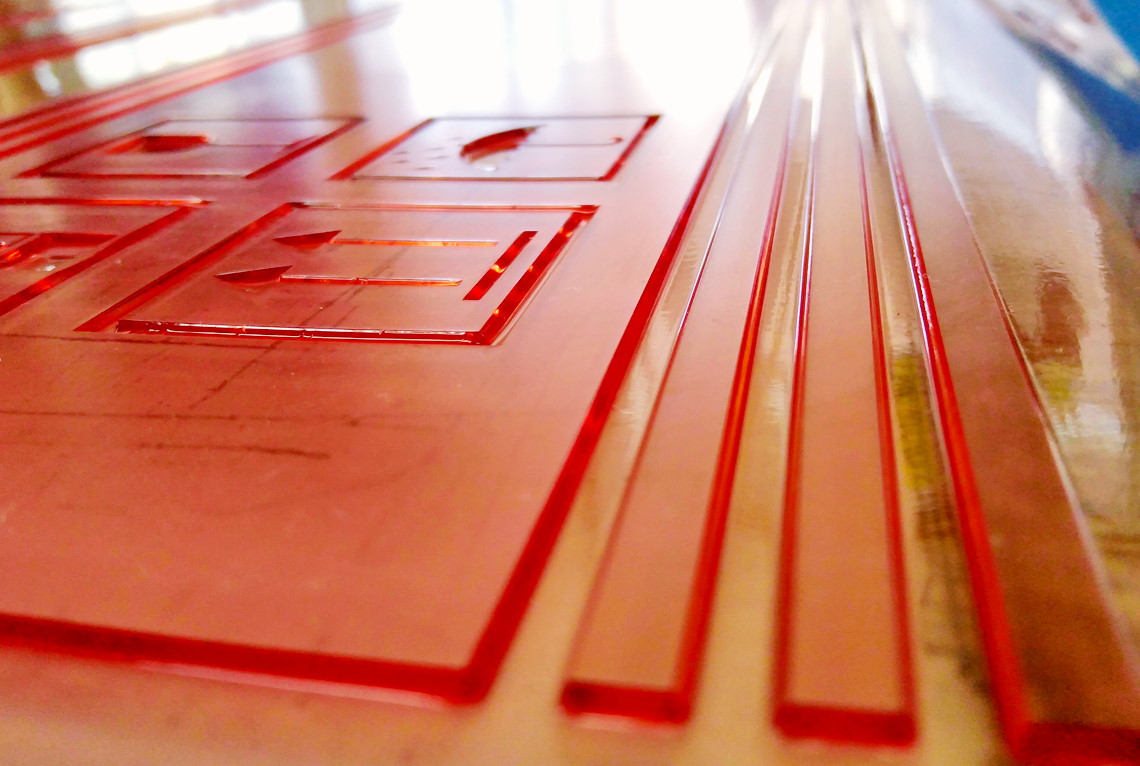
Plates
Gelatin plate is a photopolymer sheet. When this sheet is exposed to light with short wavelengths, it is converted into polymer. After completing and preparing, the graphical file is transferred to the plate section and the plates are made regarding the number of required colors.
The films are placed between the light, and It is specified which parts should be convex. After being exposed to light for a certain time, they enter another stage. The plate is washed by a specific solvent. The required parts for printing are retained and other parts are washed away, exfoliated and deepness is reduced. Then, it is dried and ready to print.
Plates are responsible for transferring the ink to the desired material and the amount of ink and their transmission percentages are directly related to the correct way of preparing the plate.
Today, with advanced technology, we are witnessing the production of very precise plates with excellent ink transfer rate. Flexo printing has been upgraded due to these advanced plates.
Printing Proof
The proof is the pre-printing sampling with original metrics to control images, contents, dimensions and sizes, which is done several times during the designing and printing process. Firstly, when the graphical process is completed, the first proof is produced using calibrated systems and advanced technology, which specifies all the requested items from the graphics department.
The second step is taken after the cylinder or plate is prepared, which is generally done on the main material and for final control and investigation of possible errors on cylinders and plates. In this stage, the dimensions, text and color intensity of the image are examined.
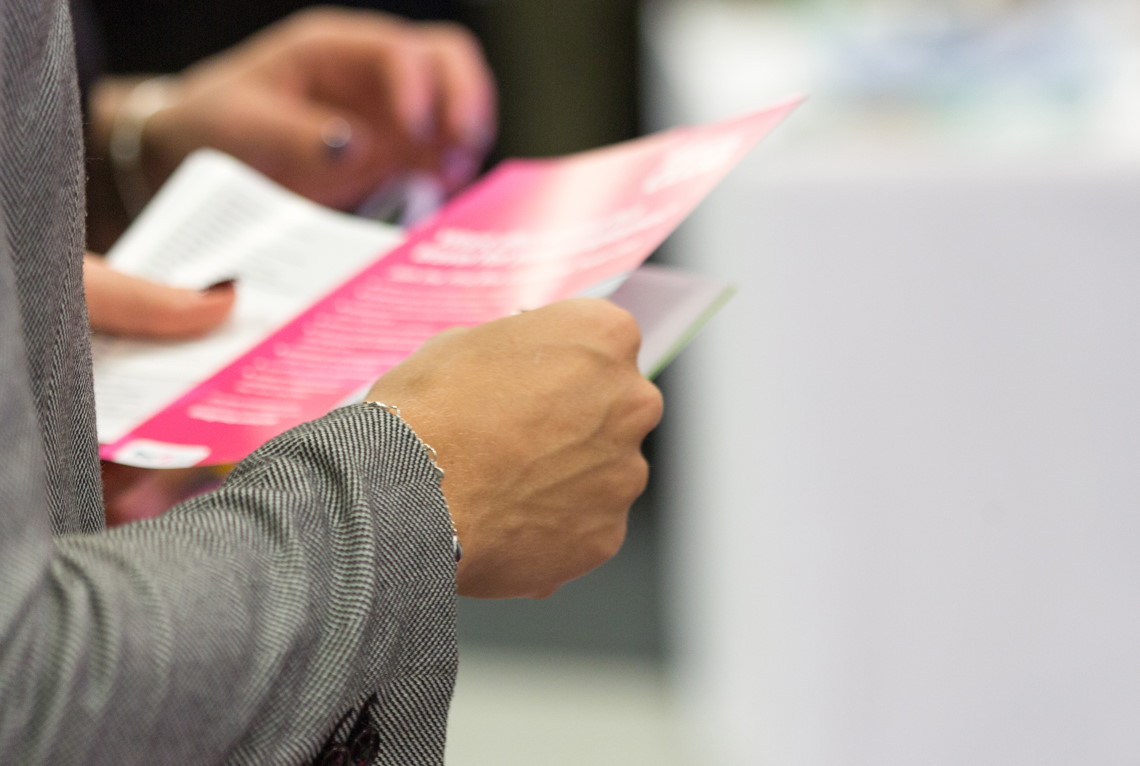
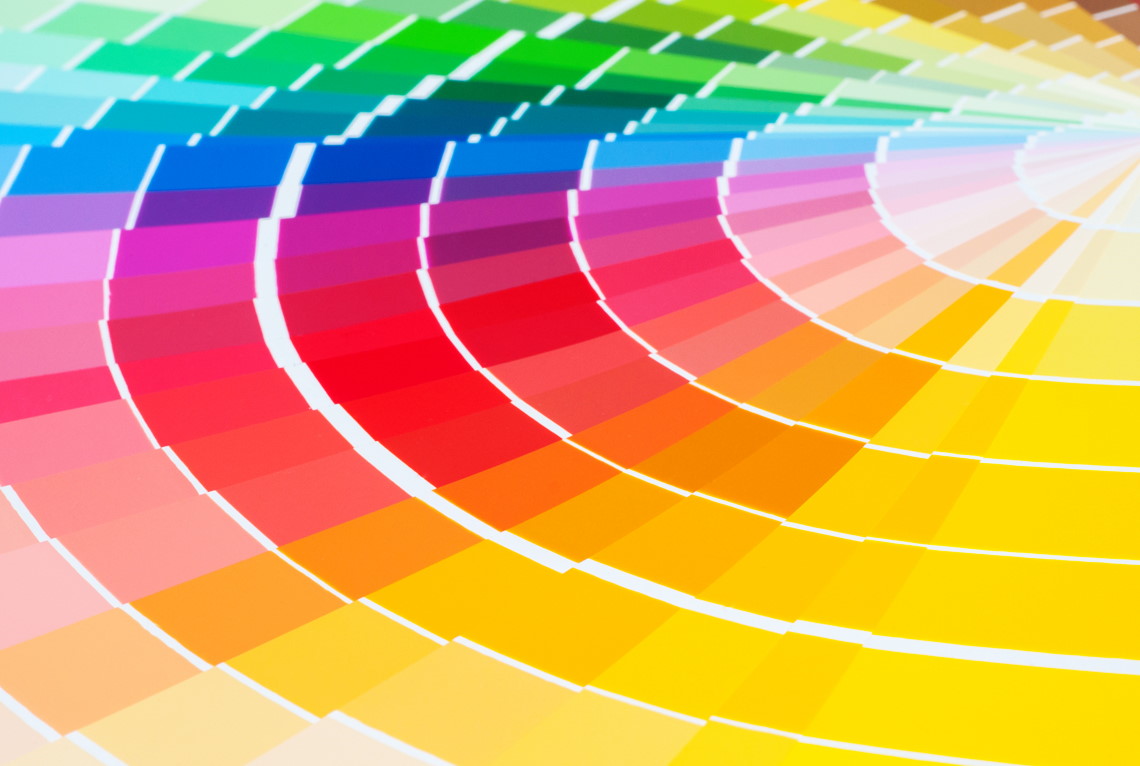
Inks
Inks are a chemical compound which has different fluidity depending on the printing process, which can be liquid, solid or powder. Their fluidity depends on the type and ingredients of the compounds. These ingredients are composed of four main:
1. Pigment:
Pigments are the main materials in determining the color of inks. After combining with resin and solvent, these colored grains move on the surface in liquid form, and these pigments made of organic compounds, lose their proper chemical structure due to heat and pressure and need suitable environmental conditions.
2. Resin:
Resin is a chemical that is combined with pigments to move it smoothly on surfaces and also makes it stick to the printing surface.
3. Solvent:
Solvents in ink, are liquid or substance such as water, oils, alcohol, etc. Which resins and pigments are dissolved in, making ink diluted.
4. Additives:
Additives are materials such as anti-foams, fillers, etc. each add a special feature to be used for different purposes in printing.
In printing industry, the mixing and grinding method and the size of pigments in the ink are highly important.
Film Production
Film production is generally done in two ways:
tubular co-extrusion and casting.
In tubular co-extrusion method, the raw materials of polyethylene or polypropylene are mixed with the necessary additives and pigments and enter the extruder. Due to the high temperature, these materials are melted and mixed together in the extruder path. After these steps, the material enters the mold to turn into solid.
After exiting the mold, the material is cooled and formed. Then, over a distance, are passed through the necessary rollers and converted to polyethylene or polypropylene.
In the last step, after passing through the corona system, they are wrapped as rolls and ready to be used.
These products are generally used in a variety of advertising shopping bags, freezer bags, garbage bags and multi-layer pouches for a variety of packaging products.
In casting production method, raw materials will enter the extruder after the specified route and the materials will be melted due to high temperature (about 250 °C) and after passing through the extruder is both completely melted and mixed thoroughly and finally enters the mold to form. Then it is flattened on a cold roller and is frmed to solid. In the following path, after adjusting the thickness and passing through the rollers, pass through the corona system and prepare to be rolled and consumed.
Packaging of food, health and pharmaceutical industries are the main consumers of this type of polypropylene and polyethylene materials.
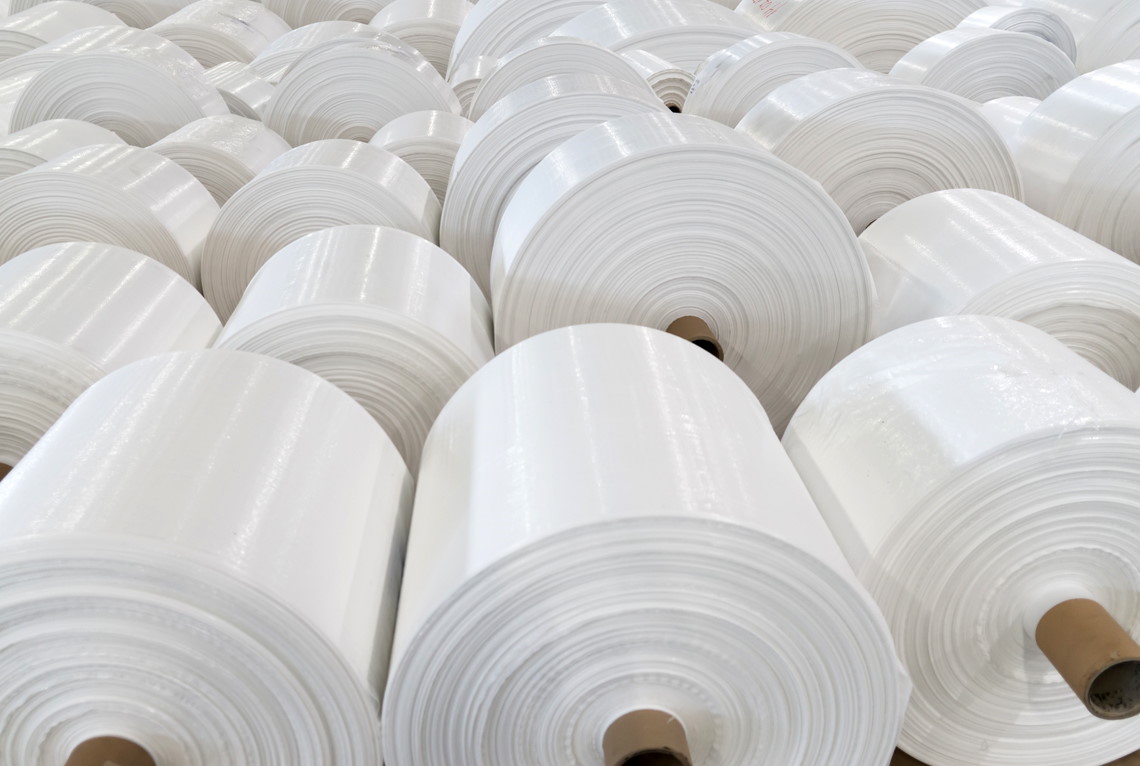
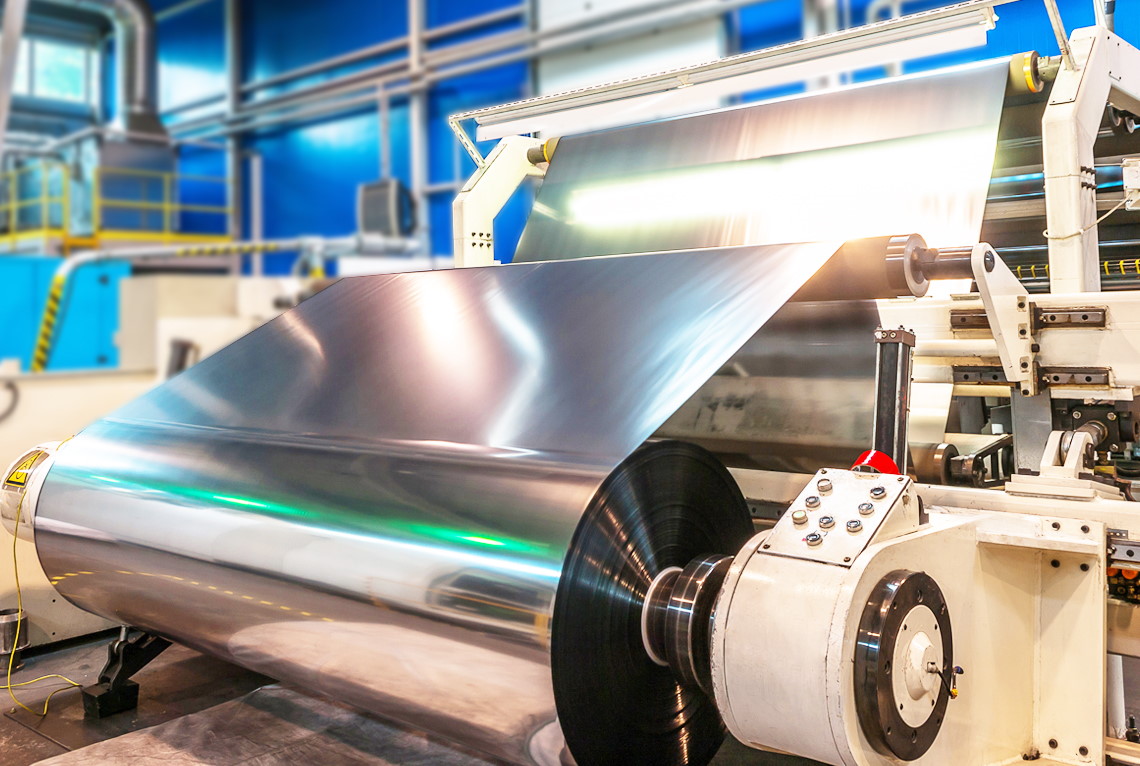
Lamination
Lamination originally means making a material in different layers. The combined material will thus become stronger, more durable and altogether with higher quality.
The reasons for using multilayer materials is not only strength and beauty but increasing the shelf life of food products.The number of laminated layers of products may be in two, three or more layers. To laminate the layers, two types of adhesive can be used, each has its own application:
- Solvent base adhesive
- Solvent less adhesive
Lamination is done when the type and amount of the glue is specified according to the main material, and the second layer passes through the rollers impregnated with glue, sticks to the main material and passes through the rollers that perform the lamination operation.
Generally, after lamentation, it takes between 24 and 48 hours for the adhesive to be dried and ready for the slitting.
Quality control
Quality control is an operation set such as measurement or examination performed on a product to determine if it matches the technical specifications.
The main discussion of quality control is sampling of products, inspection of those samples and generalization of the results to the total accumulation of the product, which is done based on statistical methods. Other method used in quality control is controlling the production process instead of controlling the product, which is done by statistical methods.
In printing and packaging industry, controlling the entry of raw materials according to the approved sample is very important.
When printing, the content, dimensions and intensity of the color are regularly checked and performed during the printing process at different intervals.
In Lamination unit, the amount of the adhesive is evaluated regularly based on the heat and curing period.
Creating constant and comprehensive database of all production processes is one of the most important QC task which can be referred to at different times.
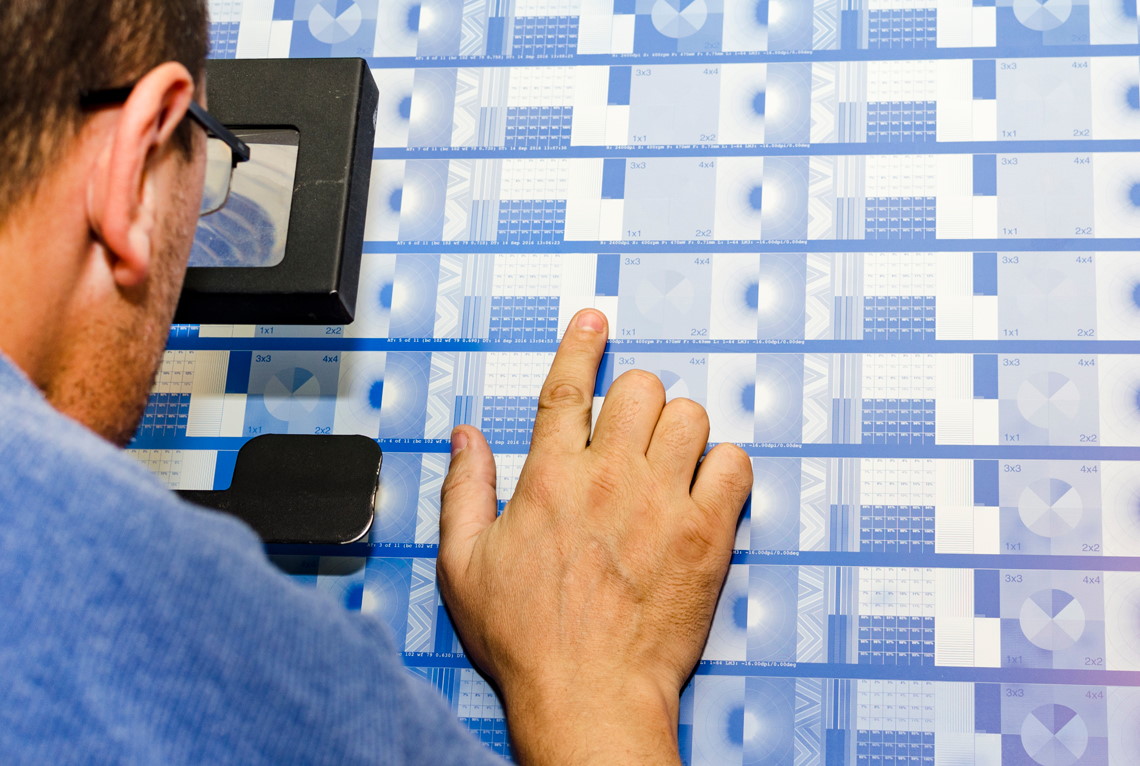